Optima RS
Seeder | Pneumatic precision drill
Ready for high performance and utmost precision
The rigid and solid Kverneland Optima RS pneumatic precision drill for high performance and output.
The advantages of this Pneumatic precision drill
Solid and easy frame design Flexible adjustment to different row widths Complete function control from the cab GEOCONTROL and GEOSEED ISOBUS intelligenceDescription
The Optima RS rigid frame pneumatic precision drill has been designed for farmers and contractors looking for a solid and efficient solution. The Optima RS frame is available in working width from 6.1m to 9.3m.
It can be adjusted to different row widths, starting from 35cm to 80cm in even and uneven configurations with up to 18 rows. It can be equipped with the full range of Kverneland sowing units: Optima HD-II, standard or tandem sowing unit in mechanical or e-drive II version.
The Optima RS frame can be fitted with a large 2000l fertiliser hopper or combined with a front hopper. In addition, the electric-driven micro-granule applicator micro drill is available.
For safe road transport, a strong lengthwise transport device is available
Features
For mulch and conventional sowing
- Optimal depth control even under extreme conditions, due to the heavy basic weight of the sowing unit with the possibility to add additional pressure (up to 100kg) onto each individual sowing unit via the spring-loaded system.
- Effective ground contour following, due to the large lateral depth control by open gauge wheels (Ø410mm, width 120mm).
- Precise seed placement by the small coulter which forms a clean furrow. Optional with quick-fit coulter tip to quickly exchange between standard layout for maize and the XHD coulter tip for sugar beet. Light re-compaction and seed covering is done by the intermediate press wheel (as option: heavy stainless steel) and the multi-adjustable V-press wheel – to ensure maximum field emergence.
Seeding heart without seals for HD-II
- The patented seeding heart by Kverneland has reduced maintenance costs to a minimum.
- No friction, no wear, low drive torque, minimum maintenance: The seed disc rotates in the seeding heart together with the vacuum chamber. This seeding drum is connected to the vacuum fan via a hollow shaft.
- This seed heart principal results in no loss of vacuum, and therefore a low vacuum requirement
- Stable design, modular system, low maintenance costs, high degree of wear resistance and optimum depth placement.
- For fertiliser placement Kverneland supplies hoppers for different applications.
- The chain drive for metering can be adjusted from 106 to 390kg per hectare at a distance between rows of 75cm.
- The fertiliser applicator is driven centrally by an easily accessible side mounted gear box.
- Fertilising coulter, standard seeding with narrow coulter design and stable, reliable construction, coil spring protection from sideways forces
- Mulch seeding notched double-disc coulter for blockage-free and precise fertiliser placement by a Ø 350mm notched double-disc Coulter.
Micro-drill for Optima HD-II and SX sowing units
The demand for microgranule applicators is increasing. Micro nutrients and also small amounts of insecticides or fungicides ensure the best start of the crop.
The electric driven micro-drills for the Optima HD-II and SX sowing units have been designed as backpack behind the sowing units and offer a hopper capacity of 17 liters.
They are electrically driven and ISOBUS controlled. The metering device consists of a wear-resistant plastic housing with exchangeable cell wheels made of stainless steel. This ensures the precise metering of the micro granules.
Operator’s safety
The engineers had focus on highest level of operator’s safety by offering easy and safe handling of the applicator. Therefore, the operator can exchange the cell wheels even when the hoppers are full of micro granule. There is no need to empty them first, reducing the operator’s risk of getting in direct contact with the granules.
A plus for the environment
The micro granules fall freely into the seed furrow without any air support, minimising the emission of dust. Therefore, the new micro-drill fully complies with the current guidelines for emission control of any granules applied.
Precision Farming
The comfortable, fully ISOBUS integrated control system allows the adaption to the stop and starting points of the seed row. This ensures precise shutting on and off at the end of the field and in tramlines (without overlaps or faults).
GEOCONTROL - Cost saving with immediate payback
Seeding with GPS and GEOCONTROL in combination with an electric driven precision drill is a major step towards precision and cost saving. These machines are all equipped with ISOBUS technology which with the help of the IsoMatch Tellus terminal, can be easily controlled.
Each electric driven seeding element, in combination with GPS and GEOCONTROL, is automatically switched on or off in exactly the right place, ensuring there is no overlap with any row that has already been seeded. This is especially handy in triangular fields, on curved or irregular shaped headlands.
GEOSEED - Precision at high end
GEOSEED is the precise synchronization of seed placement across the full working width of the machine. This ensures that seeds are distributed evenly, achieving an optimal pattern—either parallel or diamond-shaped—across the soil surface. The positive effects of this technology are far-reaching. By enhancing seed distribution, GEOSEED maximizes the efficient use of key resources such as nutrients, water, and sunlight, fostering optimal plant growth. Additionally, this uniform planting pattern helps reduce the risks of wind and water erosion, as the even distribution of plants improves soil structure and coverage, leading to better water retention and minimizing soil degradation.
Kverneland Sync – The Implement Gateway
Always Connected – Easy and Direct
With Kverneland Sync, your seeder is continuously connected to Kverneland’s online services. Designed for efficiency and ease, Kverneland Sync ensures seamless data transfer to IsoMatch FarmCentre and Kverneland ServiceCentre, optimizing your seeder's connectivity for better machine management.
Remote Service – Minimize Downtime
Kverneland Sync offers remote diagnostics, allowing technicians to quickly analyze and address electronic issues on your seeder from a distance via the Kverneland ServiceCentre. This feature helps to minimize downtime in the event of a breakdown. See how it works: Always connected
Task Management – Enhance Reporting and Transparency
Kverneland Sync provides all relevant data in IsoMatch FarmCentre, our integrated farm management platform, enabling real-time tracking, performance measurement, and secure data storage. This is especially useful for machine cooperatives, streamlining logistics and invoicing. Additionally, Kverneland Sync enables geofencing to help protect your seeder against theft, with an accumulator that allows you to locate your planter even when it’s not connected to a tractor.
Precision Farming
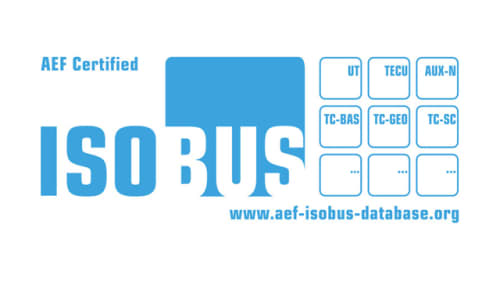
When deciding what equipment to purchase, it is not always easy to find the optimal solution in the broad market offering of today. Technology is developing fast and tractors and implements are more and more equipped with high tech electronics. We understand this complexity and are committed to provide you with easy farming solutions. Therefore these cost-efficient ISOBUS Universal Terminals, IsoMatch Tellus PRO and IsoMatch Tellus GO+ are made for easy machine control and efficient farming.
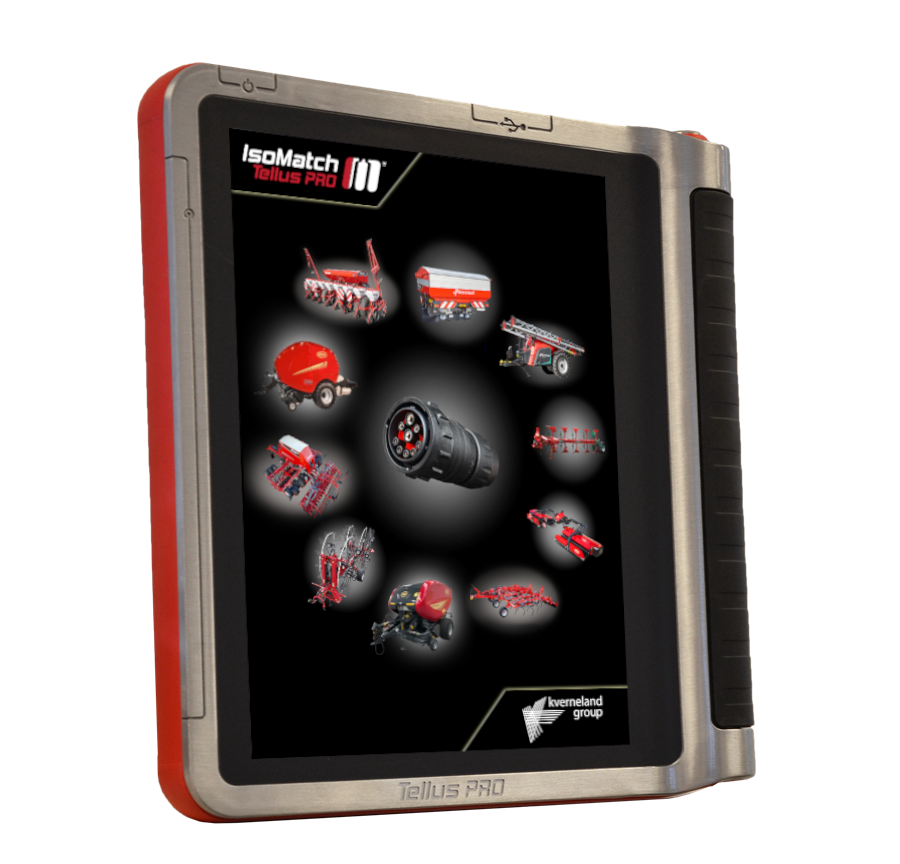
With its advanced hardware and software features, the IsoMatch Tellus PRO provides the optimal precision farming solution for an all-in-one control system inside your tractor cab.
IsoMatch Tellus PRO is the centre for connecting all ISOBUS machines and a platform for running precision farming applications. It offers everything a farmer needs to get the maximum out of his machines and crops, as well as cost savings in fertiliser, chemicals and seeds by using automatic section control and variable rate control. With the unique dual screen functionality it gives the farmer the opportunity to view and control two machines and processes simultaneously.
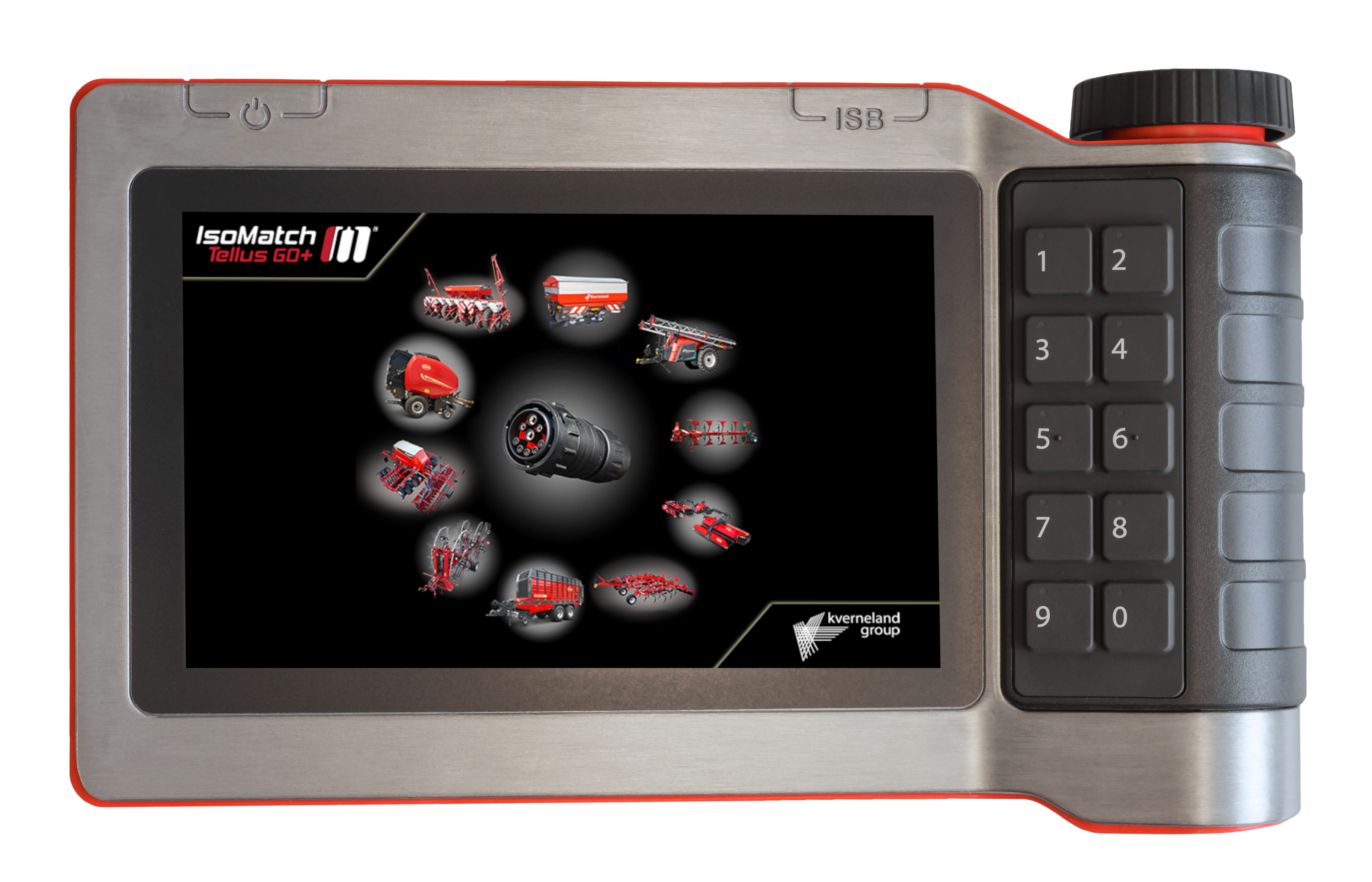
Work easy. Be in control.
IsoMatch Tellus GO+ is especially developed for controlling the machine in a simple way. The farmer is in full control of the machine in exactly the way he wants. Easy set up the machine with the soft keys via the 7-inch touch screen. And, optimal control while driving, just use the hard keys and rotary switch. Controlling the implement has never been so easy.
This can be you your first step into Precision Farming
IsoMatch Tellus GO+ makes it easy to control any ISOBUS machine from your tractor cab. IsoMatch GEOCONTROL enables you to achieve higher yields, lower costs and do your work with less hassle. This licence key is divided in two parts, Section Control and Variable Rate Control, which are available from the IsoMatch Shop. Now you can buy the specific functionality that you need.
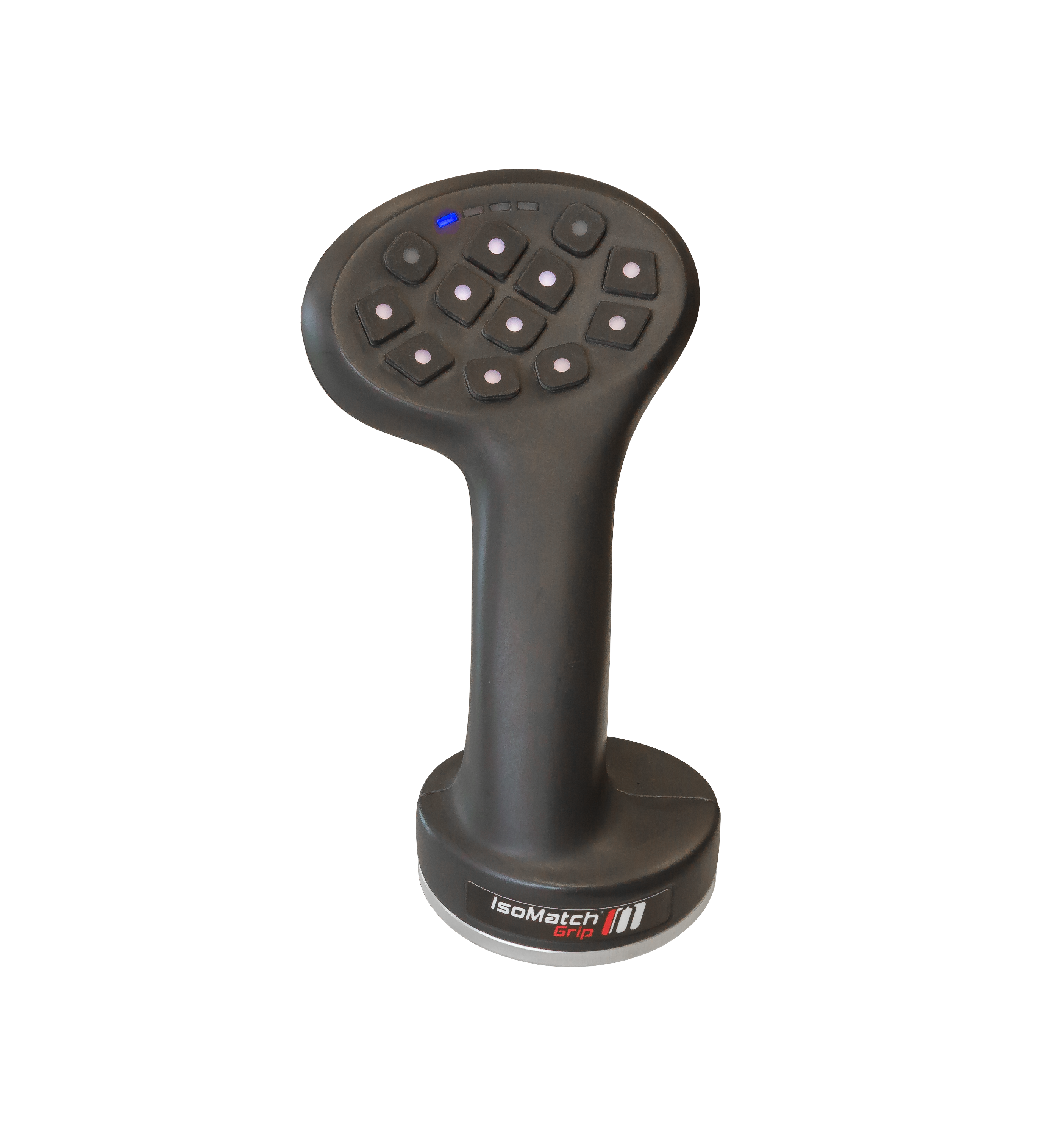
The IsoMatch Grip is an ISOBUS auxiliary device developed for great operator comfort and efficient machine control. Its ergonomic shape and the complete freedom of assigning and controlling a total of 44 implement functions from one device are unique in the market today. From your fingertips you have endless possibilities to operate all machine functions as desired. And assignments are saved per machine making it even more applicable to your needs.
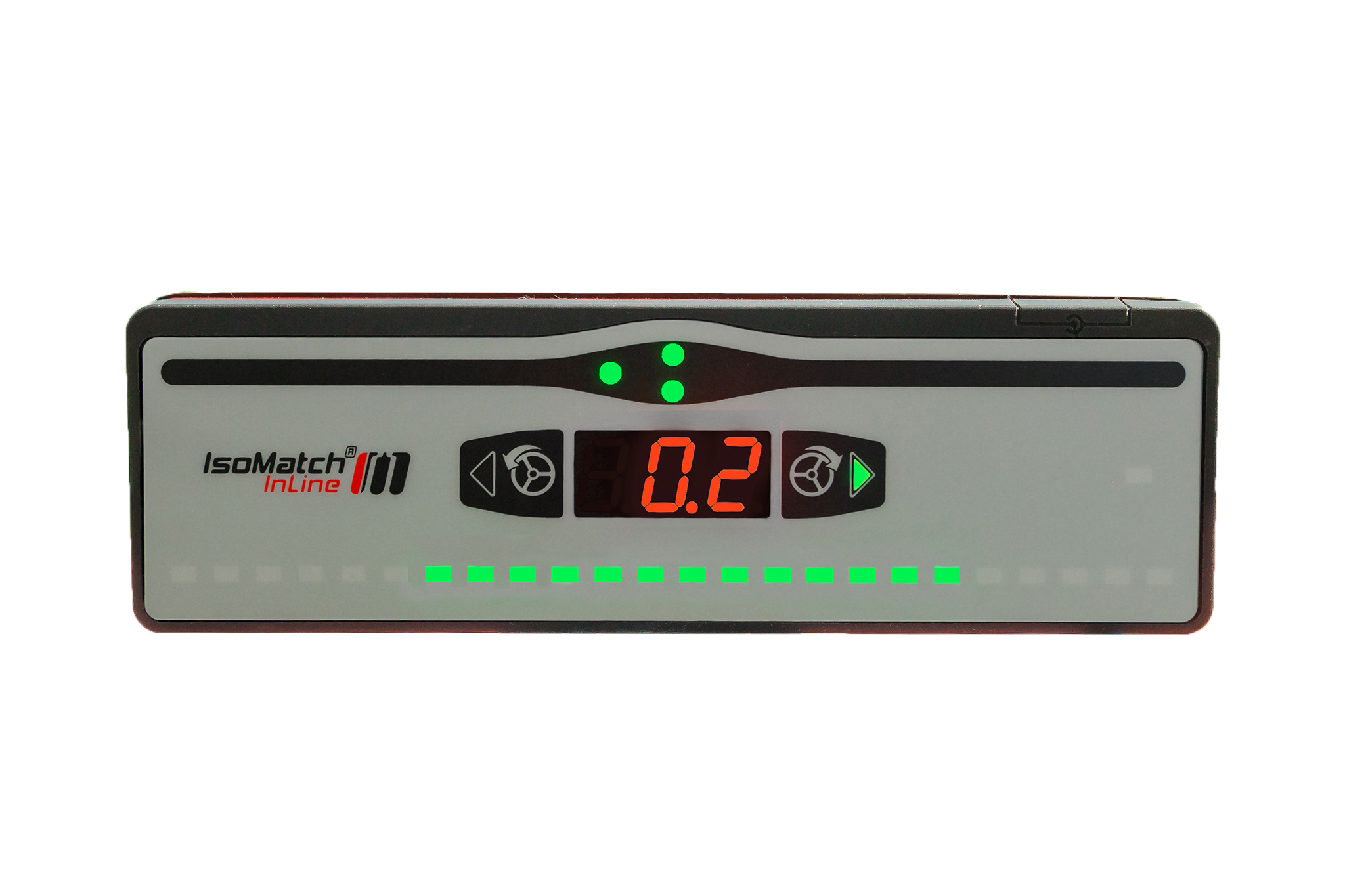
With manual guidance you are perfectly on track.
The IsoMatch InLine is a light bar which allows easy manual guidance. It is the perfect assistant to get you as close as possible to your desired A-B line. Mounted in the line of sight, you can easily see the distance from the A-B line and to which direction you should steer for the ideal position. The display of the IsoMatch InLine also displays the status of the machine sections, which adds more comfort of use. The LEDs can be dimmed for night operation.
SMART
Distance to A-B line with LED indication and a numeric display
EFFICIENT
Manual guidance in combination with IsoMatch GEOCONTROL
EASY
Displays status of machine sections
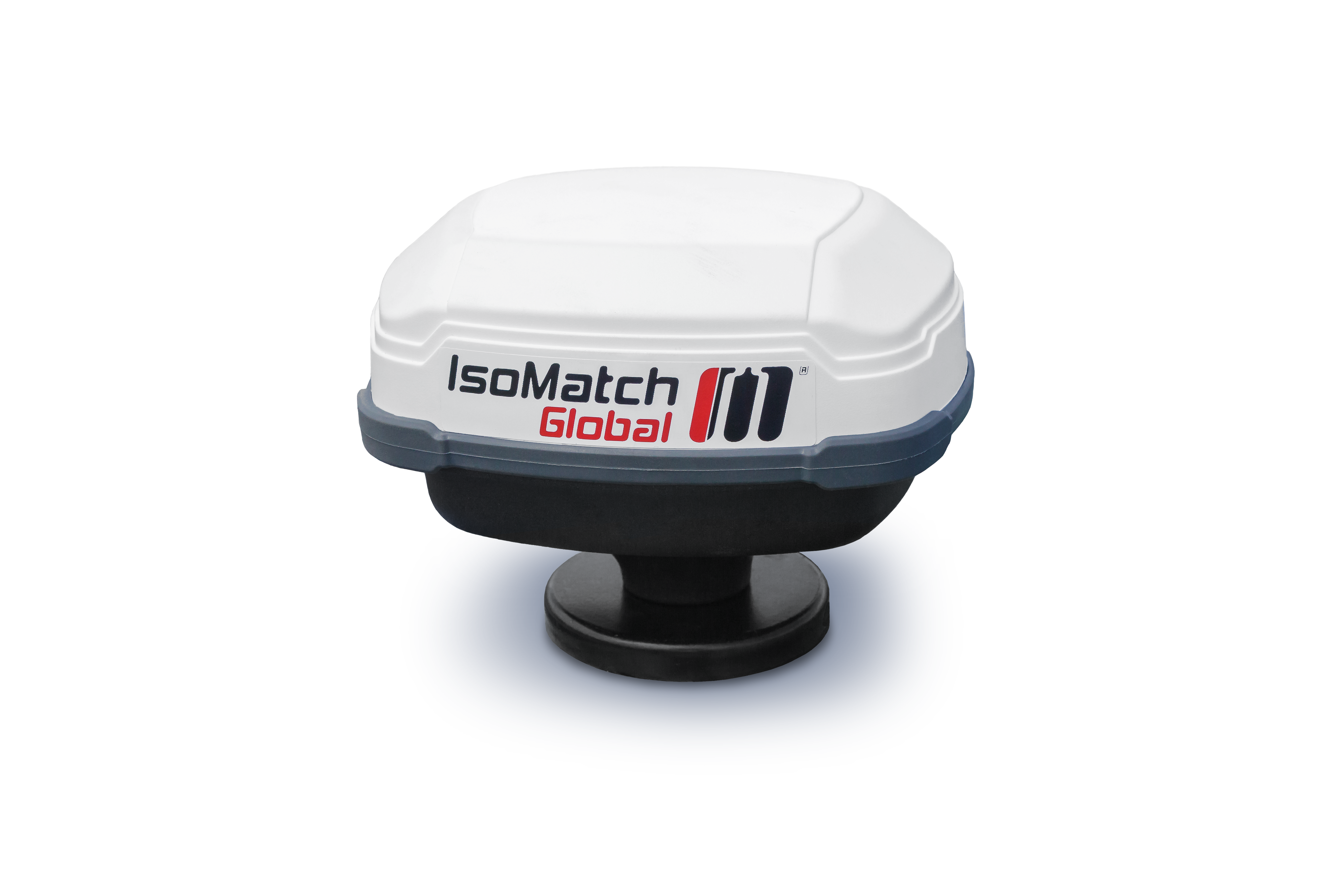
The essential accessory for IsoMatch GEOCONTROL.
The IsoMatch Global 3 is the GPS antenna, with DGPS accuracy, in the IsoMatch product range. It enables satellite navigation for site-specific section control, variable rate application, manual guidance and field registration.
SMART
Allows manual guidance, automatic section control and variable rate in combination with IsoMatch GEOCONTROL
EFFICIENT
DGPS accuracy without additional subscription fees
EASY
Easy to fit with mounting brackets included
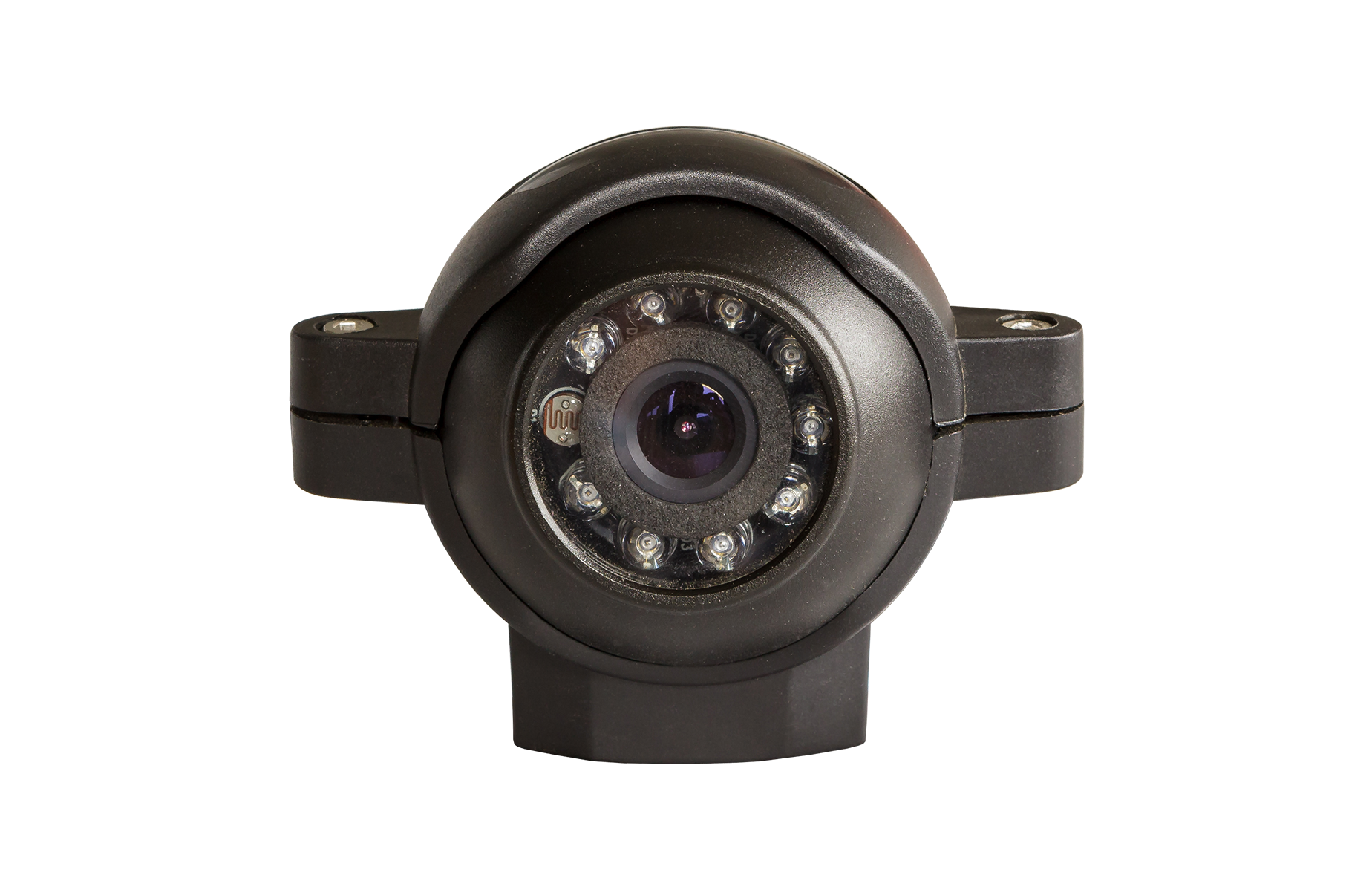
The IsoMatch Eye is the camera option in the IsoMatch product range.
IsoMatch Eye is a camera that has been developed for use with our sophisticated IsoMatch Tellus GO+ and IsoMatch Tellus PRO dual screen terminal. The IsoMatch Eye is switchable from rear view to standard view.
It gives you full control and overview of entire machine operation during day and night, because of its night vision by integrated LED’s. This increases the safety e.g. when reversing the machine or manoeuvring around obstructions.
SMART
Changeable from rear view to standard view
EFFICIENT
Full control and overview of entire machine operation
EASY
Night vision by integrated LED’s
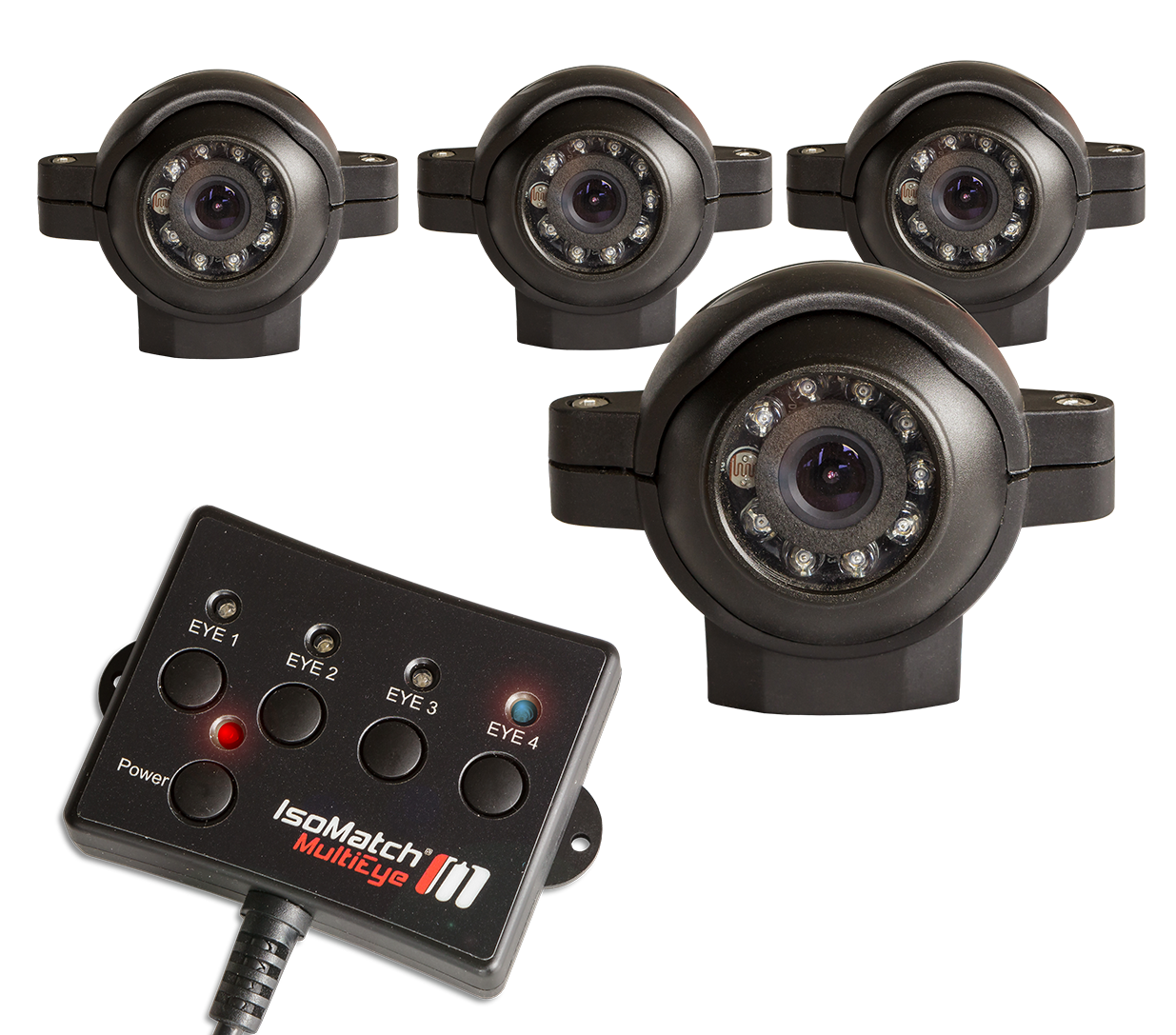
IsoMatch MultiEye is an accessory for connecting multiple cameras to the IsoMatch Universal Terminal.
With the IsoMatch MultiEye you can connect multiple cameras to the IsoMatch Tellus PRO or IsoMatch Tellus GO+ Terminal. You can easily switch between the cameras without the need for an additional screen in you tractor cabin. It gives you full control and overview of the entire machine operation during day and night, because of its night vision by integrated LED’s. This increases the safety when reversing the machine or manoeuvring around obstructions.
SMART
You can connect up to four IsoMatch Eye cameras and easily switch between the cameras with the remote control box which is standard included.
EFFICIENT
Full control and overview of entire machine operation from every side you want.
EASY
Night vision by integrated LED’s which increases the safety when reversing the machine or manoeuvring around obstructions.
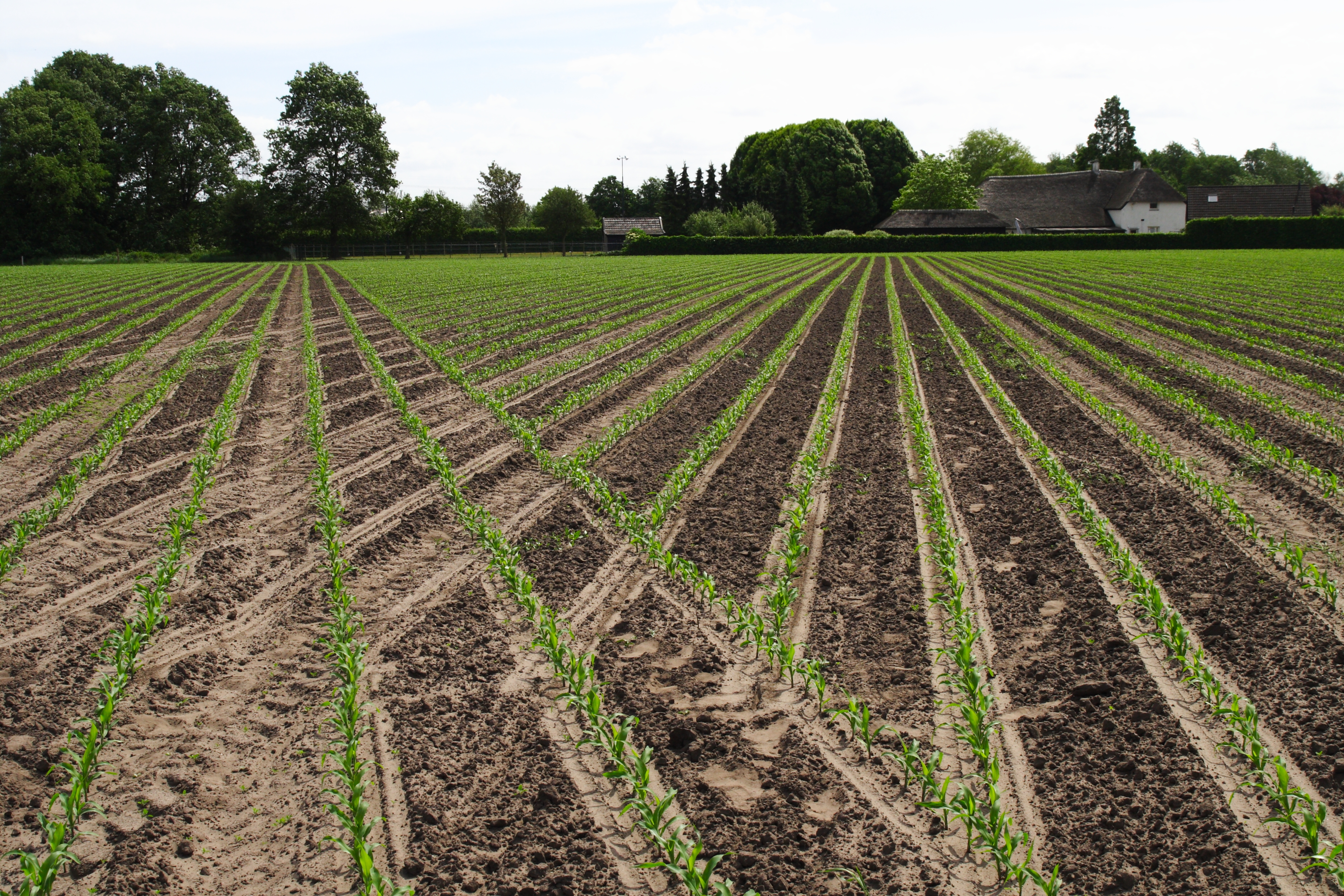
Made for smart, efficient and easy farming
IsoMatch GEOCONTROL is an advanced software application within the IsoMatch Tellus PRO and IsoMatch Tellus GO+ that helps you to control all ISOBUS compatible Kverneland Group machines such as sprayers, spreaders and seeders! Combined with a GPS receiver it fulfils the future needs in terms of easy, smart and efficient farming!
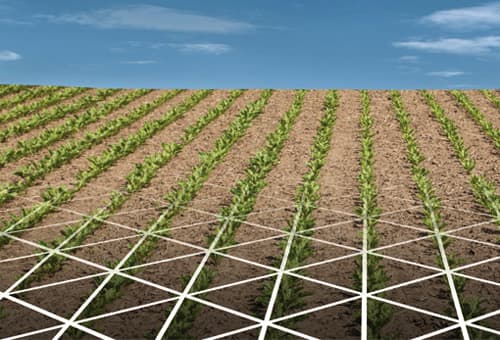
GEOSEED increases the yields of row crops and ensures maximum efficiency. Seeds are placed perfectly in line and in relation to each other.
GEOSEED is offered in two different levels:
GEOSEED Level 1 is the synchronization in the machines working width. This improves the distribution of seeds up to perfection in parallel or diamond pattern: Positive effects are the best use of nutrients, water and sun. Also the wind and water erosion is decreased.
GEOSEED Level 2 is the synchronization in the whole field. This is the necessary requirement for interrow cultivation, also across the seeding direction. GEOSEED is the only system in the world, that makes this mechanic weeds control possible!
Technical specifications
Technical specifications
Download brochureModel | Optima RS | Optima RS | Optima RS | Optima RS | Optima RS | |
---|---|---|---|---|---|---|
Frame type | rigid | rigid | rigid | rigid | rigid | |
Working width (m) | 6.10 | 6.80 | 7.60 | 8.30 | 9.30 | |
No. of HD-II sowing rows | 8 - 12 | 8- 16 | 12 | 12 - 18 | 12 - 18 | |
Row width HD-II row (cm) | 45-80 | 35-80 | 65 | 45-70 | 50-80 | |
Transport width (m) | 3.00 | 3.00 | 3.00 | 3.00 | 3.00 | |
e-drive II, ready for GEOSEED® | Standard | Standard | Standard | Standard | Standard | |
Fan drive 1000rpm | Option | Option | Option | Option | Option | |
Fan drive 800rpm | Standard | Standard | Standard | Standard | Standard | |
Hydraulic fan drive | Option | Option | Option | Option | Option | |
Linkage | CAT III / CAT IV N | CAT III / CAT IV N | CAT III / CAT IV N | CAT III / CAT IV N | CAT III / CAT IV N | |
Tyres 7.00-12AS | Option | Option | Option | Option | Option | |
Tyres 26x12.00STG | Standard | Standard | Standard | Standard | Standard | |
Hydraulically operated track marker | Standard | Standard | Standard | Standard | Standard | |
Hydraulically frame ballasting kit | Option | Option | Option | Option | Option | |
Mounted fertiliser spreader | Option | Option | Option | Option | Option | |
Maximum no. of rows with mounted fertiliser spreader | 18 | 18 | 18 | 18 | 18 | |
Mechanical drive of fertiliser spreader | Standard | Standard | Standard | Standard | Standard | |
Electro-hydraulic drive of fertiliser spreader | Option | Option | Option | Option | Option | |
Fertiliser hopper capacity in litres | 2,000 | 2,000 | 2,000 | 2,000 | 2,000 | |
No. of rows with front hopper f-drill / iXtra LiFe | 8 - 12 | 8- 16 | 12 | 12 - 18 | 12 - 18 | |
Micro granule applicator micro-drill | Option | Option | Option | Option | Option |
Technical specifications
Technical specifications
Download brochureWorking width (m) |
6.1 |
6.8 |
7.6 |
8.3 |
9.3 |
Number of rows |
8 - 12 |
8 - 16 |
12 |
12 - 18 |
12 - 18 |
Row width (cm) |
45 - 80 |
35 - 80 |
65 |
45 - 70 |
50 - 80 |